THE RESULT: Simplified wiring, combined with data acquisition located closer to the source, produce stronger and cleaner signals to bring about a substantial increase in resolution.
Durability
Durability is a hallmark of the TDAQ design. In the nine years since the TDAQ was introduced, almost 400 have been deployed and only 10 have failed!
Small Size
TDAQ's small size makes it possible to mount TDAQ anywhere on the TUO. Positioning TDAQ close to sensors means less cabling and electrical interference, which equates to higher resolution and more accurate repeatability.
Single PC Connection
A single PC connection sends digital data to the TTOC machine controller via a single 100-Mbit channel. This simplifies TTOC’s hardware footprint, which translates to even more cost savings.
Modular Design
TDAQ's modular design provides measurement capability adequate for any standard TUO. For TUOs with grinders, easily add a second TDAQ to the system with no loss of performance.
High Speed
High speed data sampling and control logic operates at 16,000 times per second (63µs reaction time), making it the perfect drop-in replacement for high-speed testing as well as standard TUOs.
Higher Resolution
Consider the layout of a traditional test machine fully equipped with force measurement and grinding capability
(see figure 1). One glaring issue here is that wires must be run from each transducer and sensor down to the main control panel, where a PLC can process and act on data. This design is poor in that it overuses wire ways, leaving designers with no choice but to place dirty, high voltage drive lines near sensitive analog data lines--sometimes for as long as 10 to 15 meters.
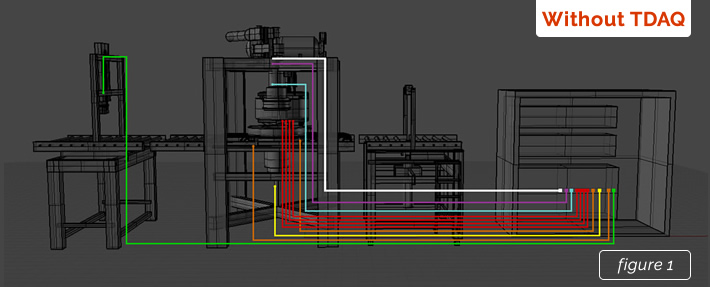
Our search of industry standard devices did not yield any acceptable solutions that matched up with this unique machine configuration and specialized complexity. So we decided to look smaller--to see what modern digital components were available and if those components could be integrated into the next big thing. Success came a couple of years later with the release of our "Tire Data Acquisition" (TDAQ) system, which has now become an integral part of the TTOC6 control system family.
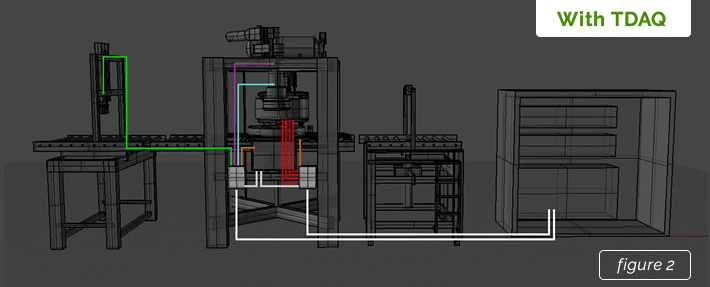
In a machine controlled by TTOC6
(see figure 2), one TDAQ becomes the central hub for load cells and pressure transducers, while another TDAQ directly controls the grinding movements based on sensor feedback. Instead of the many wires leading back to the control panel, each TDAQ only requires two: one 24VDC power cable and one Ethernet cable for transmitting test data. Not only does this simplify wiring, but performing data acquisition physically closer to the source provides stronger and cleaner signals, bringing about a substantial increase in resolution.
TDAQ Family of Products
In 2008, we originally designed TDAQ to do one thing and one thing well: tire testing.
Since that time we’ve expanded TDAQ into a product family that includes the TDAQ-XT (Crosstalk Compensator) and the TDAQ-SSI (Synchronous Serial Interface), which provide specific solutions for customer-identified input or control requirements not already supported by TDAQ and TDAQ-LC.
Designed for Scalability
- For the majority of tire testing machines, pair a TDAQ-LC with a single TDAQ to deliver tire test data over Ethernet to the TTOC PC.
- For larger machines equipped with many devices such as grinders or geometry sensors, connect up to eight TDAQs. Real-time synchronization ensures that data packets from various parts of the machine arrive simultaneously at the TTOC PC, which combines them to form a single, complete image of the machine state at a rate of 16,000 times per second.
- For simple tire/wheel machines where there is no air pressure measurement involved, install a single TDAQ-LC to measure tire force data.
Benefits of Retrofit
- For machines without a servo or PLC driving the spindle, TDAQ can automatically turn on an output to stop the spindle at a specific position for marking, or even spray an ink mark at just the right location on a spinning tire.
- One TDAQ can also digitize an entire set of analog machine controls, giving machine operators pin-point precision over a once ambiguous interface.
Never in the history of tire testing has there been a more effective way to collect and analyze tire data!